In 2019, a cold chain logistics survey noted that the biopharma industry loses approximately $35 million every year due to failures in temperature-controlled logistics facilities. In many cases, vaccines, medications and related products can spend a good chunk of time in warehouses along the supply chain as they await distribution. And in that time, warehouse temperature monitoring is critical to ensure products remain viable.
What’s unfortunate is that many warehouses, even after the pandemic exposed issues throughout global supply chains, still rely on manual measures to monitor temperatures. As we’ll showcase here, that traditional approach poses significant challenges — ones that an automated warehouse temperature monitoring system helps alleviate.
Where Manual Warehouse Temperature Monitoring Falls Flat
Consider the case of a dairy product distributor that stores large quantities of product at their warehouse. One cold storage unit housing product malfunctions in the middle of the night. If the distributor relies on manual temperature monitoring, personnel won’t be aware of the problem until they come into the warehouse the next day. With the hours that have passed, that product will have likely spoiled.
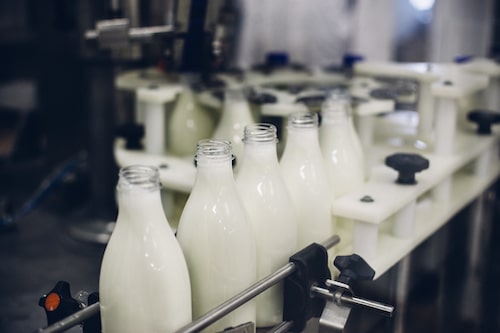
Equipment malfunctions aren’t the only issue that can cause warehouse temperature issues in off-hours. Research shows that one in four businesses experience a power outage at least once a month. Without an alert to notify personnel of the issue, dairy products can go through an extended period without refrigeration, leading, of course, to potential health risks and unsellable products.
The Power of Automated Warehouse Temperature Monitoring
There’s been a lot of recent conversation around staffing shortages in warehouses. According to one study, 73% of warehouse operators can’t find enough labor to properly staff their warehouses. This has given rise to more conversations around automation and how businesses can use it to maximize productivity.
While you can think about automation in the context of robotic systems, you can also think about it in the context of an automated warehouse temperature monitoring system.
On one hand, these control systems reduce the need for regular manual temperature checks. Employees can reallocate their time to other value-added activities and improve their overall productivity. And, when it comes time for reporting, it will be faster and easier for staff to demonstrate regulatory compliance with an automated system’s built-in reporting features.
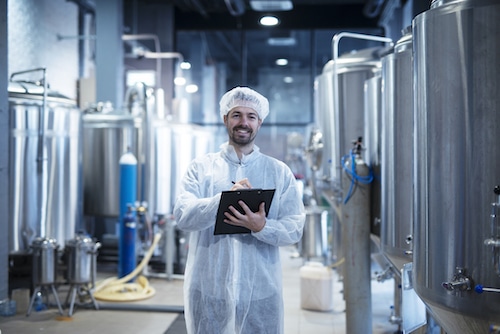
The efficiency also carries over to the speed with which personnel are able to intervene when temperature issues occur in warehouses. With 24/7 access to real-time temperature data and alerts, staff can proactively manage operational disruptions — no matter what time or day of the week. This decreases the likelihood of having to dispose of valuable inventory, as quick action can help maintain product integrity.
Choose CORIS As Your Warehouse Temperature Monitoring System
With CORIS as your warehouse temperature monitoring system, you’ll have real-time visibility into cold storage temperature conditions — with remote access anytime, and from anywhere. As our temperature and humidity sensors collect data about your cold storage units, you’ll receive instant alerts to notify you of any deviations from the specified temperature range. These alerts can be customized based on user preferences as well as issue severity.
What’s more, temperature data is permanently stored on CORIS servers. This allows you to access any historical data collected by CORIS temperature and humidity sensors to prove products were maintained in an acceptable range.
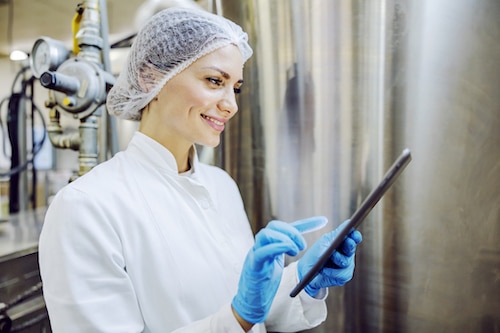
Want reliable temperature and humidity monitoring for your warehouse? Contact CORIS today. We’ll show you why CORIS is the best choice among warehouse temperature monitoring systems.